IDEC, leader in the design and construction of turnkey projects for the logistics, industrial and service sectors, is currently working on the construction of France’s biggest logistics project for CONFORAMA in Tournan en Brie (Seine-et-Marne). It is time to take a look at how work is going after five months of work on this exceptional warehouse, which measures almost 200,000 m².
Each month, IDEC offers you an opportunity to dive into the work site at this huge logistics warehouse for CONFORAMA that is currently being built by its teams in Seine et Marne. Developed with ARGAN and GAZELEY, the operation has now seen almost half of the units appear out of the ground. Last time, we looked at the installation of the concrete pillars, fire-resistant walls and the frame, so now it is time to look all the details concerning the installation of the roofing, cladding, the setting up of the concrete production unit and we meet up with Frédéric, one of the designers / project leaders for this important project.
The roofing going on
Once the frame for a unit is complete, which is the case for 15 out of the 31 units in the project, the roofers have been busy sealing up the building. The first stage involved guaranteeing safety in the workplace with a net being put in place in case of people or objects falling. The workers could then go about laying down the corrugated steel sheets and the skylights to allow smoke to escape in case of fire and to offer natural lighting in the units. Then, the building was insulated with rock wool sheets being applied. The final stage involved fitting two waterproof coats.
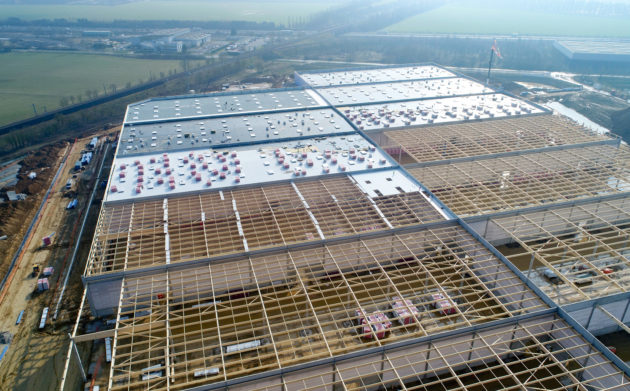
A busy pace
In order to stick to the schedule that was established in the contract, two teams of roofers are busy working at the same time on the odd and even units. They are keeping up a pace of one unit being sealed up every fortnight. One week is given over to laying down the sheets and skylights and the second is given over to fitting the insulation and making everything watertight. Five months after work first began, 5 units are already completely sealed with the aim being to complete the roofing on the first stage in a fortnight from now.
Fitting the cladding
At the same time, work has begun on fitting the sandwich panels. This cladding comprises two metal sheets separated by compressed rock wool. This covering offers two advantages: very efficient insulation, a more attractive appearance and a heat screen in case of fire with resistance to fire lasting two hours. Once the cladding has been fitted to a unit, the woodwork is added by the workers and in particular, the window strips. This work takes two days per unit, one day for the fitting of the aluminium structures and one day for the glass. The final stage before the walls are sealed involves the installation of the loading bay doors.
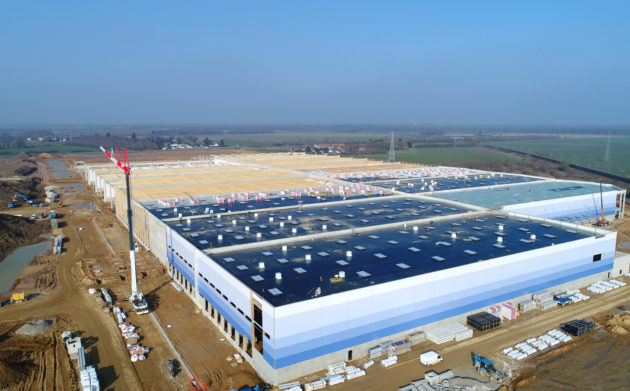
Installation of the concrete maker
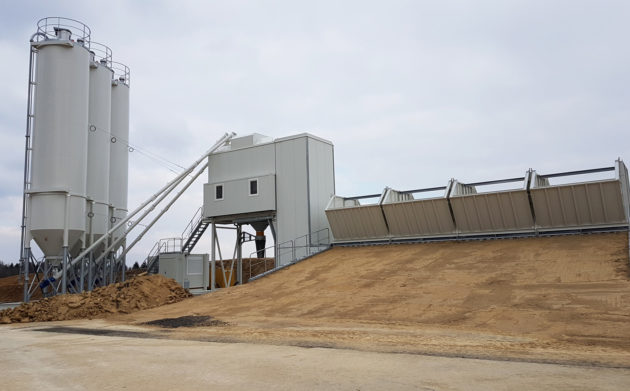
The construction of this warehouse, which measures almost 200,000 m² requires the installation of a temporary concrete production unit on the work site. After a month to set it up, the unit will enter service at the same time as work begins on laying the flooring in the units. Thanks to the ability to produce 400 to 600 m3 per day, it will be working all out to provide the flooring for the 31 units in the project, then the turning area in front of the 190 loading bay doors.
We met up with Frédéric, designer and project leader
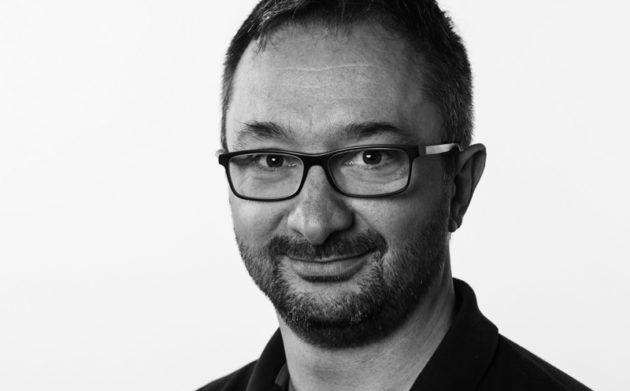
“I am in charge of making a 3D model for this operation, which is very complicated because of its size. I am in contact with all of the firms from whom I obtain the technical models that I then incorporate into our 3D model in order to identify any clashes that we may encounter with each area of work. I then update our model as required. I am also present alongside the works team each day with the help of another person to answer any technical questions. For this project we are also using an electronic data management system, which makes it easier to communicate with all those involved. My role is not just to come up with the 3D model of the building with our BIM Manager, but also to be there to help our partner firms each day, as many of them are just discovering BIM.”